No invasive sensors or new machines: real-time data without intervening in processes
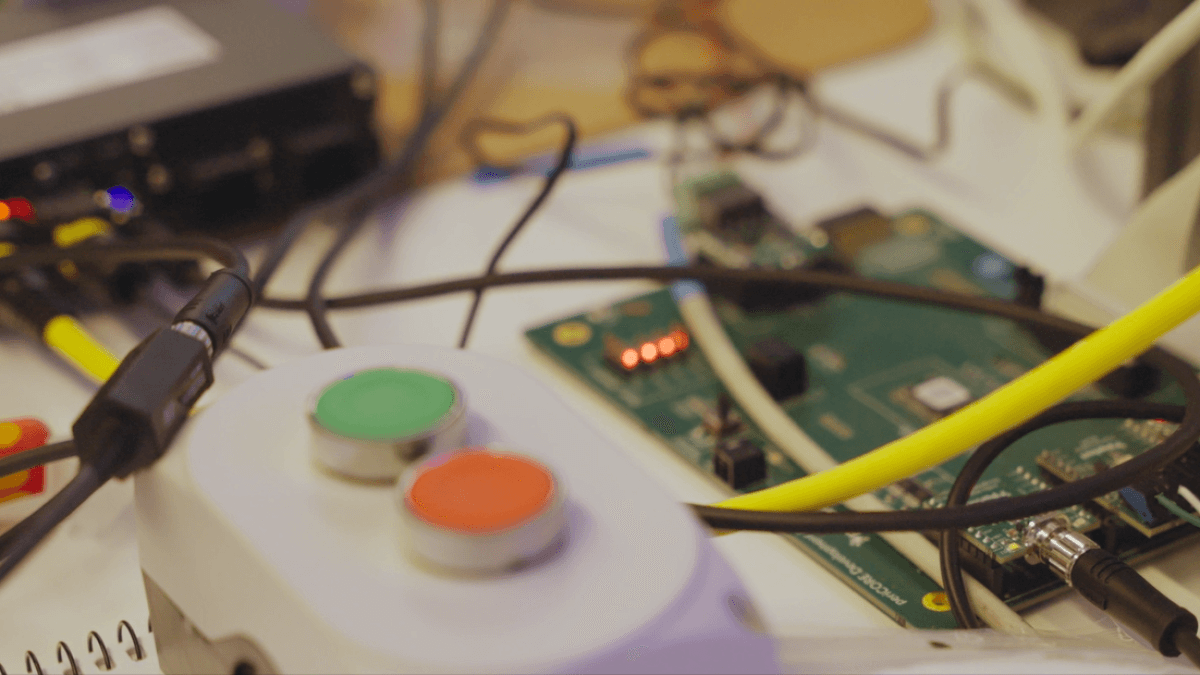
In a chocolate factory, thousands upon thousands of bars are produced every day. Until now, to know the total number of bars produced, how many were perfect or how many were defective, how many were packaged correctly or not, we had to wait until the end of the day. Now, thanks to the installation of smart adapters at the beginning and end of the production line, we can access all this data in real time, which can be crucial when making decisions (before it's too late).
Because in a company, and specifically in an industry, without data, there is no understanding of our strengths and weaknesses or our potential, and therefore no progress. Data is the most valuable asset in any industry because it provides key information about machine performance, the status of processes, and potential areas for improvement.

For example, data management directly impacts profitability: by knowing the detailed performance of each machine, inefficiencies can be identified and operating costs reduced. We can also anticipate the future and prevent problems before they occur. Real-time information, thanks to machine data extraction, allows production and maintenance managers to react immediately to any anomalies in the process, but it also affects other departments, such as sales, logistics, finance, and marketing.
"The innovative feature of this technology is that it only works on the external part of the machine, without interfering with its operation; it doesn't require shutting it down or carrying out new approvals." María Rivas, Director of Operations and Co-Founder of Zentinel MDS
A Catalan startup has devised a system to extract this data from industrial machines using pioneering technology: "We install sensors on the outside of the machinery, independently of the PLCs. These generate a signal that, thanks to smart adapters, which they process internally, is converted into data, into this valuable information. We want to help reduce the digital divide in the industrial sector and improve productivity," explains María Rivas, director of operations and co-founder of Zentinel MDS, founded in 2022 and located in DFactory Barcelona, the Industry 4.0 ecosystem of the Barcelona Free Trade Zone Consortium.
The innovative aspect of this technology is that it only works on the external part of the machine, without interfering with its operation: there's no need to shut it down or tune it up because there's no intervention inside. This is what's known as "industrial observability," the ability to interpret machine operation by analyzing its external signals to process the data locally in real time and share it with any IT platform, which will be the basis for creating and operating business applications.

This system is especially valuable in sectors where production is somewhat delicate. For example, a company that bottles water must closely monitor its production, or else there could be serious consequences. A lack of traceability could complicate the identification and recall of affected batches, whether due to spoiled water, poor-quality plastic packaging, or incorrect labeling. This would pose a risk to consumers and could lead to legal issues and a brand crisis for the company. "We generate an architecture that provides control from the start of production, that is, from the start-up of the machine to the exit from the palletizer," explains Rivas. "And another sector where our technology also makes a lot of sense is the pharmaceutical industry, since no machine is involved inside, they don't have to go through the repeated bidding and quality controls required by such equipment."
We help reduce the digital divide in the industrial sector María Rivas, Director of Operations and Co-Founder of Zentinel MDS
The most extreme example of the usefulness of Zentinel MDS's smart adapters relates to older machinery that is generating high demand in Latin America. "Imagine a robust press that was manufactured 30-40 years ago with German or Swiss precision. Time has passed, and the machine, due to its reliability, continues to function perfectly, but it's not digitalized, so we can't monitor its production while it's in action. By installing sensors linked to the smart adapter, we can record all its activity and consumption in real time and make decisions accordingly. This is how a machine that was pure iron is transformed into a 21st-century device."
Obligatory question: Now that everyone interacts daily with artificial intelligence, how does this new technology contribute to fueling it? “We are strategic for artificial intelligence because we offer qualified information, what we call “quality data,” which comes directly from the machine during production. With the data that Zentinel MDS provides, machine learning models can detect patterns in the data, anticipate equipment failures, and optimize production processes.”
A cyber-secure and sustainable technologyThe second important question is how cybersecurity is guaranteed throughout this entire process: “This is something we were very clear about from the beginning. That's why we're using a new technology that provides connectivity through a network of just two cables: one carrying data and the other carrying power. Both are connected to smart adapters, which make the process of transforming data into information local; there's no connection to the cloud or data storage centers.” We also ensure that formulations or manufacturing parameters aren't altered by a cyberattack.

This technology uses advanced encryption protocols and access control to ensure that the collected data is secure and protected from potential threats. "We are completely cybersecure. We are also sustainable, because the data transformation process is internal; we don't have to be connected to data centers, nor do we depend on large energy or cooling requirements, and therefore, our carbon footprint is zero."
This startup 's main clients are manufacturers of consumer products, such as food and beverages, pharmaceuticals, and personal hygiene. "These are manufacturers with very high production volumes where small inefficiencies in the operation of their machines could lead to significant financial losses, and where the ability to instantly understand the efficiency of their production processes is key to maintaining their competitiveness," adds Rivas.
The software and hardware function design is carried out at its headquarters in DFactory.The hardware used by this company is jointly developed in Germany, and all software and hardware function design is carried out at their headquarters in DFactory, where they moved into the company in June 2023. Five people work there, and another five work at their subsidiary in Brazil. “DFactory is an ecosystem where you can find friendly companies with which to generate technological synergies. This gives us more knowledge, more growth opportunities, and greater adaptability to the market. Since we've been here, our progress has been spectacular. I like to say that many technology companies were born in a garage; we were born in DFactory.”
"A travel agency or law firm can't be located at DFactory. To be eligible, a company must be dedicated to one of the Industry 4.0-related technologies." Pere Navarro, special delegate of the State in the Barcelona Free Trade Zone ConsortiumWhat requirements must a startup like Zentinel MDS (or any company) meet to set up shop in this hub of the Barcelona Free Trade Zone Consortium? “For example, a travel agency or law firm can't be located in DFactory. For a company to come here, it must be dedicated to one of the technologies related to Industry 4.0: sensors, robotics, artificial intelligence, 3D, etc. DFactory is based on the relationship between companies, and therefore, it's also based on being able to share these technologies. The goal is for the companies here to work together and speak the same language,” explains Pere Navarro, special delegate of the State at the Barcelona Free Trade Zone Consortium. The DFactory project doesn't end with its first building or with the 37 companies located here, which now almost fill the capacity of the first warehouse. The second phase of this ecosystem will be built next year on the site directly across from the current one, and will encompass more than 100,000 square meters dedicated to Industry 4.0.
lavanguardia